Terminal wiring harness terminology highlights introduction- [Dongguan Leyang]
source:未知 popularity:time:2020-01-04 10:19
1.Welding conditions
Introduction: General terminal harness products are usually connected by welding. Welding is the core of the entire process. The pre-weld and post-weld processes are all about obtaining products that meet the welding requirements. With the popularization of wave soldering technology, new requirements for the welding applicability of connectors have been put forward. Welding conditions are divided into: Welding conditions are divided into: 1 the weldment must have weldability 2 the surface of the weldment should be kept clean 3 use a suitable flux 4 a certain temperature and time
2.Surface plating
Brief introduction: Terminal wire harness hardware usually requires tin, gold, nickel and other surface plating treatment. Electroplating refers to a surface processing method in which a salt of a preplated metal is used as a cathode, and the cations of the preplated metal in the plating solution are deposited on the surface of the base metal by electrolysis to form a coating . Electroplating is the basic guarantee of connectors.
3.Hardware material
Introduction: Hardware refers to five metal materials: gold, silver, copper, iron, and tin. Traditional hardware products are also called "small hardware". Refers to five metals: gold, silver, copper, iron, and tin. Can be made into art objects or metal devices such as knives and swords after manual processing. The material of the terminal wire generally refers to wires, terminals and so on. The terminal hardware material performance determines the elastic performance of the contact point of the wire harness, which is a key factor in the quality of the terminal wire harness.
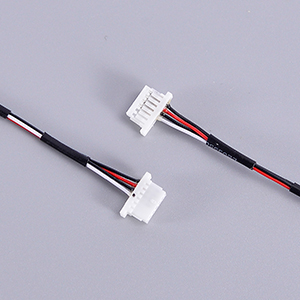
4.Plastic material
Introduction: A polymer compound polymerized by addition polymerization or polycondensation using a unit as a raw material. The main component is a resin. Terminal wiring harness products mostly use engineering plastics such as P.B.T, P.V.C, P.P.S, L.C.P, NYLON66, etc. The use of excellent plastic materials is a guarantee that the connector will work normally within the design temperature range for a long time
5.Pitch
Introduction: Usually refers to the center distance between two laterally adjacent plug points (pins) in the plug part of the terminal harness product. The unit is millimeter (MM). It is the foundation of the most important overall size of industrial connector products.
6.Insulation resistance
Introduction: It refers to the resistance value that is caused by applying a DC voltage to the insulation part of the terminal harness to cause leakage current on the surface or inside of the insulation part. English: Insertion resistance If the insulation resistance value is low, it may form a feedback circuit, increase power loss, cause interference, etc. Excessive leakage current can cause heat or DC electrolysis to destroy insulation, cause short circuit, and endanger safety.
7, insertion force and extraction force
Introduction: English: Insertion force The force required to insert a male lead into a female socket. Explanation in English: Withdraw force The force required to remove another lead from one terminal. Generally, it must be at least 0.5 ounces. Terminal harness insertion force purpose: In order to ensure the reliability and stability of the terminal harness after adaption, this standard is specifically formulated in accordance with EIA-364-13C (International Electrical Association Insertion Force Test Specification). Insertion force and extraction force, which are maintained for a period of time under a certain force, is called holding force.
8.Brine spray test
Introduction: Salt spray test: A corrosion test that tests the terminal harness plating or air tightness. It is divided into two categories, one is the natural environment exposure test, and the other is the artificial accelerated salt spray environment test. The artificial simulation of salt spray environment test is to use a kind of test equipment with a certain volume of space-salt spray test box, using artificial methods in its volume space to create a salt spray environment to evaluate the product's salt spray corrosion resistance .
Top
- The role of the terminal connecting line on electronic products- [DONGGUAN LEYANG
- Smart home appliance terminal line products and solutions- [Dongguan Leyang]
- The impact of the development trend of the security industry on the terminal line
- Wire-to-board terminal wire, although the wire is small and precise, it is good-
- Take you to know 1.0mm terminal line, high precision 0D- [Dongguan Leyang]
- Dongguan Leyang Precision Electronics Co., Ltd. Spring Festival 2020 Notice
- Talking about the development trend of China's terminal wire industry- [DONGGUAN
- Terminal wiring harness terminology highlights introduction- [Dongguan Leyang]
News
- The impact of the development trend of the security industry on the terminal line
- Take you to know 1.0mm terminal line, high precision 0D- [Dongguan Leyang]
- The role of the terminal connecting line on electronic products- [DONGGUAN LEYANG
- Terminal wiring harness terminology highlights introduction- [Dongguan Leyang]
- Talking about the development trend of China's terminal wire industry- [DONGGUAN
- Wire-to-board terminal wire, although the wire is small and precise, it is good-
- Smart home appliance terminal line products and solutions- [Dongguan Leyang]
- Dongguan Leyang Precision Electronics Co., Ltd. Spring Festival 2020 Notice